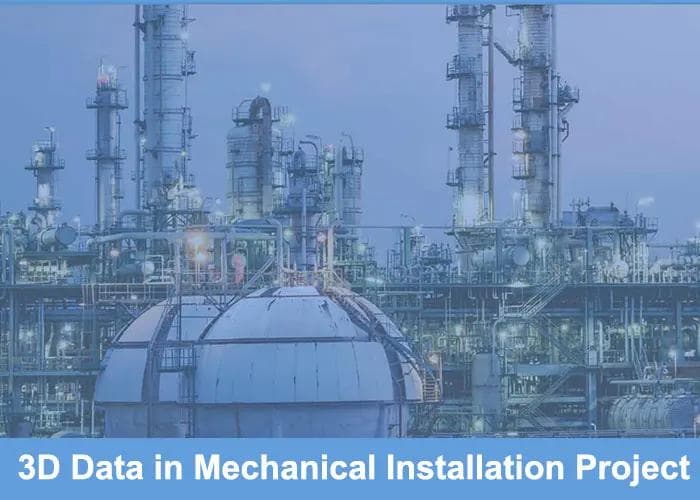
Published by:

Dalibor Vuchikj
11 Mar 2022
My vision is to support companies and organizations in the development and implementation of mechanical engineering and operational projects. As a Mechanical Engineer by education, combined with a deep passion for new technologies. Specialize in offering cutting-edge digital methods and technologies, including 3D scanning, intelligent 3D modeling, documentation, 3D data processing and optimization, analysis, simulations, VR integration, and more.
Using 3D Data In Mechanical Installation Project (Case Study)
PROJECT SUMMARY:
The client wanted to install additional equipment to increase the production, the place where the equipment being installed was tight and the production must work with full capacity most of the time. Safety should be on a high level.
DESCRIPTION:
The project team, composed of members of a company how is performing the installation work and the plant how investing, needed help in the pre-planning and planning phase of the project, in terms of creating and analyzing 3D Data, simulation of the process of installation, in a virtual environment, and producing complete technical documentation.
Mainly the client challenge was:
-Tight space in the installation area.
-Large-scale and heavy equipment to be installed.
-Miss communication with equipment vendor (design of process equipment)
-Work on height and hot work activities.
-Installation during the production.
-Short term for implementation of the investment.
-Documentation for fast and easy learning and maintenance.
GOALS:
Reduced time of planning and installation, zero-incident in the installation process, and minimal stop on the production during installation.
APPROACH
Our approach to these challenges was:
1) DIGITALIZATION
Creating 3D Data from the installation area, existing equipment, and planned equipment in CAD environment, Hight precision of capturing the real space, and processing 3D Data.
Capturing / Measurement of the installation area and existing equipment.
To have the installation area, existing equipment, and installations in cad environment we perform 3D laser scanning on the area and process to parametrical 3D Data.
Preliminary and Detailed CAD model.
Building 3D Models from process equipment, mechanical and electrical installation, from 2D drawings and specifications.
2) SIMULATION AND ANALYSIS
After the digitalization of the existing situation and the equipment that needs to be installed, the virtual model is equal to the real situation and the installed equipment, we are performing a few analyses and simulations.
3)Collision Analysis.
We perform an analysis of collisions between the existing situation and new equipment, to be sure that we will not have unpredictable issues in the installation process.
Motion Analysis
With this analysis, we are planning the method of installation, installation area, and sequence of the activities, not leaving any decision to be made by the workers, we calculate the space and the motion/transport of the equipment.
Safety Analysis
We analyze all actions of the method of installation, and we make sure that all of them will be safe, we create a safe and fast-performing system for working on heights and hot work.
4) DOCUMENTATION
For future activities, we create full documentation in 3D and 2D, with a full preview and explanation of all
equipment and installation for the project, optimized and synchronized for the easy and fast performing
in a virtual environment, they prefer.
5)As-Build CAD Model
We create a complete 3D CAD model from the equipment incorporated In the process, including all changes that occurred during installation and were different from the detailed design. We also did an inspection of the installation on the parts with crucial meaning for the process, using 3D scanning technology and BIM CAD Model.
6)BOQ Documentation
For archiving and learning needs we created complete BOQ documentation showing the models and table with all useful information about parts, assemblies, and systems, from the manufacturer, name, technical characteristic, etc.
RESULTS
With our approach to the project, we help the team to achieve the goals and to return the investment catching the increasing demand for the production. And this project was the best project for this global organization.
We help the team to reduce the LiveCycle of the project with:
-3D CAD model from the installation area saves time in communication.
-We helped the team to overcome the miss communication with the vendor of the process equipment, by sharing a CAD model from the installation area and guiding them to design the equipment, with this approach we save time and prevent issues.
-Complete analysis of collisions prevents unpredicting issues to increase the time of installation. In this project, we had a part of the equipment that was in collision with the rooftop beam, and we manage to fix this issue during the planning and build phase, this saved us time for communication, reconstruction of the part, and delivery.
-Motion Analysis helps us to manage the activities and reduce the time of installation.
-With this analysis we predict which activities can perform parallel, we defined the time to perform the activities, and manage the activities that require stopping the production, to be done a few at the same time, with this method we reduce the time of installation and reduce the stops of the production.
-Safety analysis helps us to go true all processes without incidents.
With safety analysis, we control the planned activities to go with minimal possibility for incidents, also with the system for safe work we reduce the time of installation.
-The produced 2D and 3D documents help the team easily and fast to learn and do research. In the documentation, the team can find a visual view of the element, part, a system with technical information, information from the vendor, and contact from the vendor, for fast and easy learning and maintenance.
CONCLUSION
Return of the investment of 1,200,000 dollars from 3 months reduce to 0.9 months regarding the increased demand in handover mount and enable the company added 3 months to produce extra
profit, zero incidents in the project, and ~48 hours stop of the production. With our technology and methods, we predict the potential risk, we reduce the issues, we reduce the time of installation, we increase the safety, we help communication to go smooth.