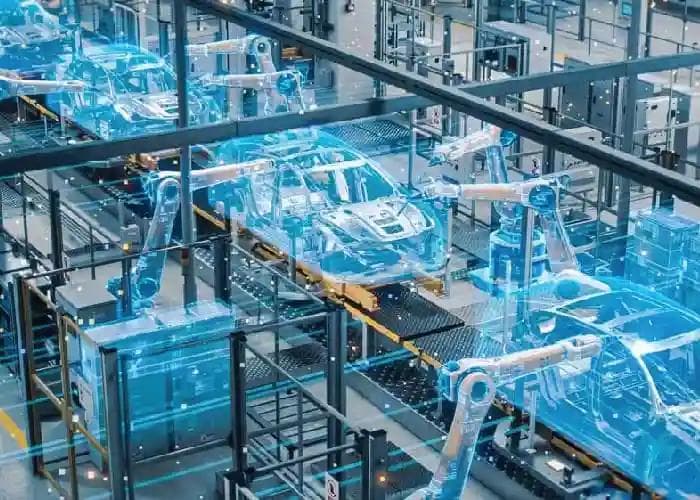
Published by:

Dalibor Vuchikj
11 Aug 2022
My vision is to support companies and organizations in the development and implementation of mechanical engineering and operational projects. As a Mechanical Engineer by education, combined with a deep passion for new technologies. Specialize in offering cutting-edge digital methods and technologies, including 3D scanning, intelligent 3D modeling, documentation, 3D data processing and optimization, analysis, simulations, VR integration, and more.
Optimizing Factory Layouts with XR Technology Virtual Reality And Augmented Reality
The Factory Layout Experience leverages Extended Reality (XR) technology to create a full-scale, immersive environment for defining, reviewing, editing, and validating shop floor layouts. This innovative approach allows teams—whether located in different offices or countries—to collaborate seamlessly, with suppliers also able to participate. By automatically uploading libraries of existing plants, tools, and equipment, teams can conduct comprehensive reviews without the need for CAD expertise.
This XR-driven experience empowers planning and layout engineers, either working independently or in groups, to optimize factory layouts. Viewing data at full scale and in context helps identify clashes, access issues, and missing elements that might be overlooked on a traditional CAD screen.
Factory floors are complex environments, often containing thousands of pieces of equipment designed externally or scanned into architectural CAD systems. To effectively understand and assess changes, it’s crucial to integrate data from various sources—be it robot cells designed in specialist CAD systems or hand tools and storage racks from mechanical CAD.
Using a 3D resource catalog, 2D factory layouts can be quickly transformed into rich 3D layouts. Advanced positioning tools allow easy movement, alignment, and snapping of 3D data. With widely used plant equipment readily available, there’s no need to design from scratch for each new layout. Simplified tools enable even non-CAD experts to participate, improving communication and collaboration.
Human-centered operations are enhanced through mannequin analysis, enabling the testing of design and operational aspects such as reachability, access, and injury risks. This ensures compliance with safety and ergonomic standards.
By enabling all stakeholders to review layouts collaboratively, companies can avoid costly redesigns. Modern manufacturing demands flexible, modular, and easily reconfigurable layouts that minimize downtime, reduce costs, and enhance product customization. The ability to conduct "what-if" studies and iterate potential solutions quickly allows factory engineers to optimize designs and share options with design engineers effectively.
Digital prototypes further validate products, ensuring that machines, plants, and factories are feasible for repair and maintenance. Visual representations of layout changes can be fed back to CAD for optimization, reducing the need for expensive on-site modifications.
By connecting people, systems, and machines in a digital thread, companies can accumulate and reuse knowledge, optimize assembly lines, and streamline production processes. All proposed changes are saved to the server, allowing staff to review updates offline, ensuring that everyone is informed and aligned.