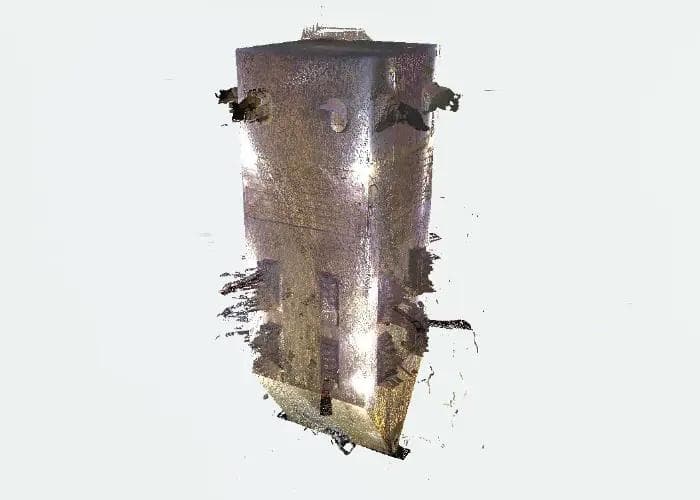
Published by:

Dalibor Vuchikj
1 Aug 2021
My vision is to support companies and organizations in the development and implementation of mechanical engineering and operational projects. As a Mechanical Engineer by education, combined with a deep passion for new technologies. Specialize in offering cutting-edge digital methods and technologies, including 3D scanning, intelligent 3D modeling, documentation, 3D data processing and optimization, analysis, simulations, VR integration, and more.
Leveraging Advanced 3D Technologies for Efficient and Precise Technical Analysis
Modern technologies and methodologies enable efficient and detailed technical analyses within a short timeframe. In this blog, we describe a method that allowed us to conduct a documentary analysis by collecting parametric data in just 12 hours and processing it within 7 days. This approach yielded results that prompted further analyses and identified potential future defects.
During a regular shutdown and overhaul period for a thermal energy-based electricity production facility, we were tasked with performing a deformation analysis. This analysis was crucial for a feasibility study aimed at documenting data, drawing conclusions, and encouraging investments to rejuvenate and extend the facility's lifespan.
Given the brief shutdown period, we employed laser scanning technology to collect data from the entire interior of the industrial furnace. The collected data was transformed into a point cloud, representing the structure in detail.
We then processed the parametric point cloud data to create a parametric 3D CAD model, optimized for use with SOLIDWORKS. The accuracy of the point cloud data in representing the real situation was within ±1mm, and the discrepancy between the point cloud and the 3D CAD model was within ±5mm.
We verified the accuracy of the point cloud and the CAD model by comparing cross-sections every 50 cm in a 65-meter-high furnace. Deformation analysis was conducted by comparing the detailed design CAD model with the as-built CAD model created from the scanned data, with accuracy checks also performed every 50 cm.
This method allowed us to quickly gain insights, foresee the need for additional resources, and identify potential future defects, thereby removing uncertainties. The documented data serves as evidence for requesting additional funds and predicting future issues.
Implementing this method annually or during each overhaul would enable the creation of models that predict facility operations and potential problems over an extended period. By comparing and processing data with the aid of artificial intelligence, we can achieve more accurate predictions.
This method is particularly beneficial for facilities with significant environmental impact. It ensures better control and prediction of the facility's future responses, contributing to environmental safety.