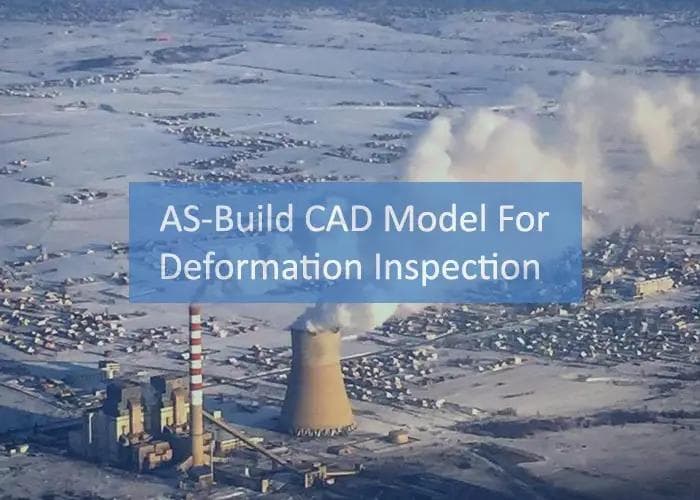
Published by:

Dalibor Vuchikj
12 Apr 2021
My vision is to support companies and organizations in the development and implementation of mechanical engineering and operational projects. As a Mechanical Engineer by education, combined with a deep passion for new technologies. Specialize in offering cutting-edge digital methods and technologies, including 3D scanning, intelligent 3D modeling, documentation, 3D data processing and optimization, analysis, simulations, VR integration, and more.
Successful Creation of a Digital Twin for Kosovo B Power Plant
We are excited to announce that during the recent regular shutdown of the Kosovo B Power Plant, In 3D Technology was commissioned to create a digital twin of the furnace in its cold condition.
Our task was to process and generate 3D data that would be accessible to the engineering team on standard computer systems (regular laptops) and be used for deformation analyses in the future.
To create this digital twin, matching the physical parameters of the real furnace and the 3D CAD model, we undertook the following actions.
This project presented several challenges. First, the limited access to the furnace required precise planning and expertise. Working in extreme conditions necessitated a thorough risk assessment, coupled with stringent health and safety procedures and protocols developed by our team and approved by the client’s team.
We captured the furnace's interior environment using 3D laser scanning at 15 measured spots over 12 hours. This process generated a high-resolution point cloud with HR 360 color pictures, capturing the entire environment in great detail. From this data, we created a high-resolution poly mesh.
To ensure the 3D data was easily accessible on all computer systems, we developed a CAD model with solid structures optimized for use in SOLIDWORKS. This model maintained the integrity of 3D objects and was organized into groups for ease of use.
Creating a SOLIDWORKS-friendly CAD model involved developing a method to produce 3D data that closely matched the point cloud and the real furnace. We are pleased that our efforts provided the client team with the data needed to perform deformation inspections, comparing the detailed design CAD model of the furnace with the as-built 3D model from the point cloud.
We believe this analysis will assist in better and faster planning of future actions.
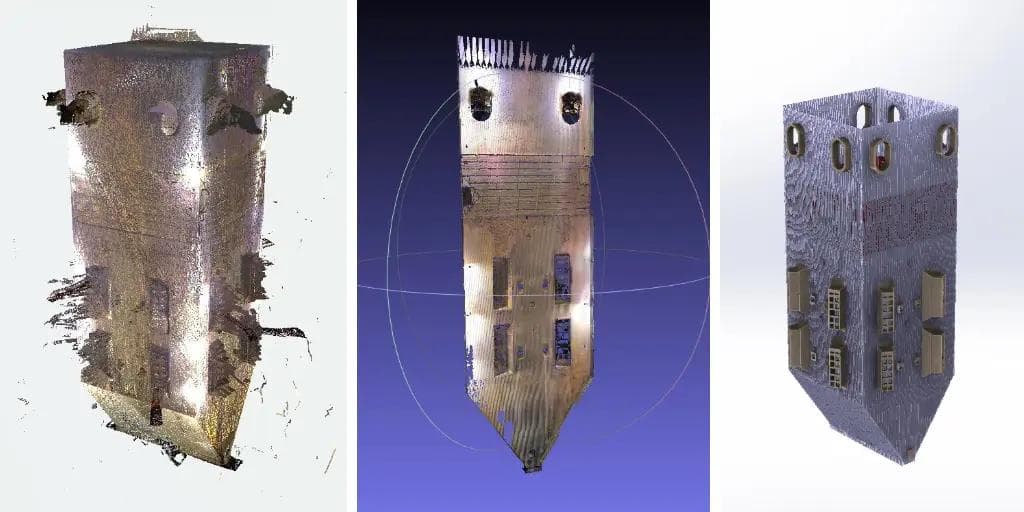